Advanced Inspection
Applications- NII as replacement of IVI
- Pressure Vessels
- Pipelines
- Pipework
- Structures
- Subsea
- Heat Exchangers and Tubing
- Turbines
- Data Science
- Equipment integrity and reliability
- Robotic Tank Inspection
- Internal Inspection of Caissons
Turbines
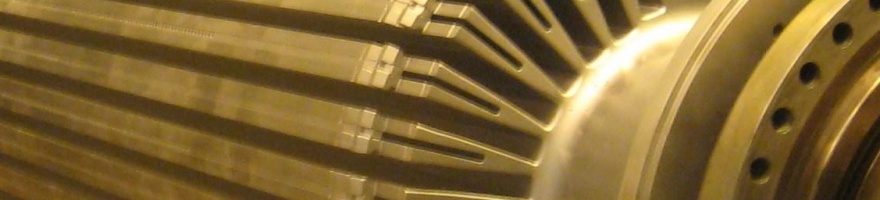
The most critical flaws in terms of effect on the remaining life of the rotor are bore surface-connected fatigue cracks. For more than a decade, Sonomatic has been providing fully automated hollow rotor bore examination services to customers worldwide. Our newest Boresonic system reliably and accurately detects and sizes near-surface fatigue cracks as well as processing flaws in hollow turbine and generator rotors.
Our unique focused probes nearly eliminate the near-surface dead-zone, which is so prevalent in other systems. An automated high frequency Eddy Current surface exam is performed concurrent with the UT examination. The Sonomatic boresonic system is capable of examining bores from 2 to 10+ inches in diameter. Many bottle bores and steps can also be reliably inspected.
GETIL1292
Large GE steam turbine generator rotors and 324 generator rotors with diagonal flow cooling are prone to potential cracking in the rotor tooth dove-tail area due to fretting (the relative motion between the wedge and slot dovetail). Experienced Sonomatic technicians can detect minute cracking before it propagates into something more serious. When the wedge bars are removed, wedge slots are carefully examined using a specially designed surface eddy current probe. And for those situations where it is impractical to remove wedge bars, specialized ultrasonic techniques have been developed.
Solid Rotor Bore Examinations
Sonomatic has developed specific ultrasonic techniques for evaluating axial and circumferential indications from the external surface of solid turbine rotor bores. Specific applications vary depending on configuration, failure mechanisms, etc. However, typically, a combination of Pulse- Echo and ToFD (Time-of-Flight Diffraction) techniques are used. We are adept at designing specialized techniques to fit almost any application. Sonomatic has recently used similar techniques to inspect submarine propeller shafts for circumferential-radial cracking resulting in detection of 1mm deep indications up to 8 ft away.
Generator Retaining Ring Examinations
Generator retaining rings are subject to high operational stresses which may result in stress corrosion cracking when poor environmental conditions are present. Traditional inspection methods require extensive dismantling of the plant, and even standard ultrasonic techniques require the rotor to be removed from the stator.
Sonomatic offers fully automated inspections utilizing digital data storage and displays that can be performed with the rings attached, removed, or even in-situ. In-situ inspection offers considerable time savings and cost benefits to our customers. Retaining rings may be inspected by the Pulse Echo Eddy Current and/or ToFD techniques. The precise Eddy Current used depends upon the particular design of the retaining ring.
Turbine Disk Bore Inspection
Turbine disk bores are subject to circumferential radial cracking at the disk-bore to rotor interface. In addition, the keyways are subject to heavy stresses which may allow fatigue cracks to originate and propagate. Sonomatic developed a multi-tiered approach to inspecting disk bores/keyways. A combination of manual Pulse- Echo, Automated Pulse-Echo and Automated ToFD scans are performed based on a scan-plan developed for each individual disk to achieve 100% coverage of the critical areas. Disks and keyways can typically be fully inspected at a rate of one disk per shift or faster.
Dovetails
The problem with blade root inspection is that the scanning surface changes constantly with probe position and there are numerous direct and indirect geometric responses. This renders interpretation very difficult and many beam angles are required to provide full coverage. The Sonomatic approach is to use a very small, high output transducer with a wide beam spread to flood the blade root with energy, and image the responses using grey-scale imaging technology. By utilizing a miniature scanning frame, which is hooked on to each blade in turn, a characteristic set of signals are generated. Cracked roots show disturbances or a different pattern of signals.